AUV Cuttlefish
Dual-arm intervention AUV Cuttlefish
Technical Details
Size: | Ø 2.8m x 2.0m x 0.8m |
Weight: | 1200kg |
Speed: | 4 kn |
Actuation/ Engine: |
Thruster: 8 x Ring thruster, Wittenstein Cyber Motor GmbH, thrust 500N, diving depth 6000m
|
Whole System Diving Depth: |
Initial 300m, depending on the configuration
|
Maneuverability: |
6 DOF freely selectable orientation and travel attitude
|
Manipulation: |
two deep sea capable arms (pressure compensated):
4-DOF docking arm with ball head gripper
• Extended length 1,710mm
• Integrated WLAN antenna
• Tensile load: max. 1kN
6-DOF working arm
• Length extended without gripper: 1.680mm
• Payload: 7kg
|
Battery / Capacity: |
2x LiFePo 5 KWh 50V
|
USBL: |
Evologics S2CR 18/34
|
DVL: |
Rowe Technology SeaPilot 1200kHz
|
IMU: |
iXblue Phins C3 (fiber optic)
|
Pressure sensor:: |
Absolute sensor Keller PAA-33X 10bar
|
Obstacle avoidance: |
Tritech Micron DST CHIRP Sonar
|
Cameras: |
3 x Basler ACE 2040-25GC (1x front, 2x bottom stereo)
|
Lighting: |
2 x Bowtech LED-K-Series headlights
|
Onboard computers: |
Intel i7-8700 @ Kontron mITX-CFL-S (Navigation, AI, Evaluation), Supermicro X10SDV mITX (Storage, Backup), 3x Odroid XU4 (lowlevel behavior)
|
Organisational Details |
|
Sponsor: | Federal Ministry of Education and Research |
Grant number: | Funded by BMBF, grant no. O1lS17029A |
Application Field: | Underwater Robotics |
Related Projects: |
Mare-IT
Information Technology for Maritime Applications
(08.2018- 11.2021)
|
System description
In addition to fully autonomous operation, it is possible to operate the vehicle in a hybrid mode using an optical fiber, where the power supply is integrated into the system but the vehicle can be remotely controlled or monitored for critical operations on underwater structures. For this purpose, the vehicle has a variety of optical and acoustic sensors for environmental awareness in addition to the manipulators.
Videos
CIAM: Exploring the Challenges of Docking Procedures with a Remotely Operated AUV
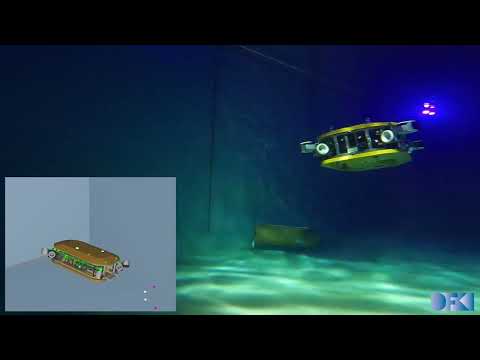
Autonomous underwater vehicles (AUVs) are already being used to inspect structures in deep waters. However, the systems are still accompanied by large supply ships, launched at sea, and retrieved – a risky and, at the same time, costly undertaking. Together with partners from industry and research, DFKI is developing intelligent AUVs in the joint project CIAM (“Cooperative Development of a Comprehensive Integrated Autonomous Underwater Monitoring Solution”). These systems are capable of covering large distances and monitoring deep-sea installations at different locations without the use of additional ships. The energy supply (and prospectively also the capture of broken-down underwater vehicles as well as the exchange of information) is to be ensured by actuated charging stations, which can be sent out as needed and dock autonomously to the systems. The video shows experiments in the large saltwater basin of the DFKI's Maritime Exploration Hall in Bremen. Until the actual hardware is available, the AUV Cuttlefish, which is technically similarly equipped, serves as a placeholder for the charging station and the tube as a placeholder for the target vehicle. The docking procedure, which is still manual here, is a highly complex operation even in calm waters. To check afterwards how exactly this process has worked, the positions of the Cuttlefish and the tube can be tracked live with the aid of a Qualisys motion tracking system. For this purpose, several reflective spheres are attached to the surfaces of the systems, which can be tracked by a total of twelve cameras with UV emitters.
Mare-IT: Powerful IT infrastructure for underwater maintenance with ground-breaking dual-arm AUV
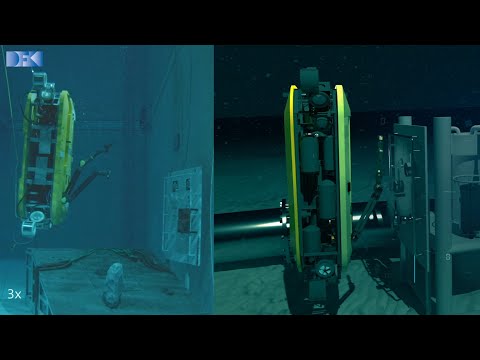
The project Mare-IT focuses on enhancing the information flow between underwater robotic systems, subsea assets, and land-based control stations to integrate inspection data in business information systems. The targeted scenario is realized with the recently developed autonomous underwater vehicle (AUV) Cuttlefish, which is equipped with two robotic arms to interact with subsea structures.